EX (max. density: 2.4)
POLYex
Intermediate Bulk Container
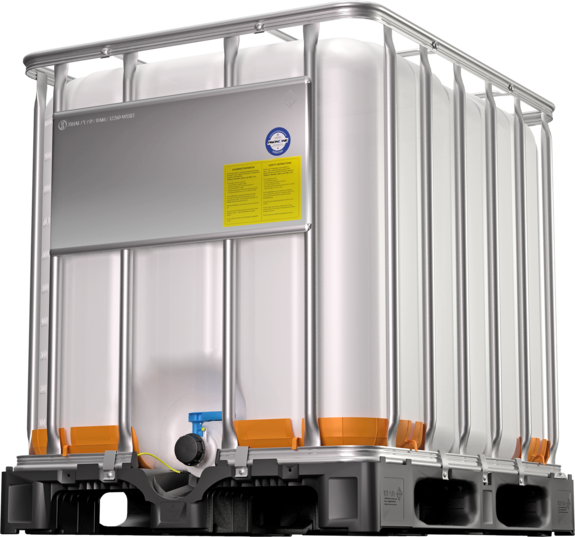
POLYex IBC
Versions & accessories
POLYex IBCs are UN tested and approved for filling with flammable liquids and use in EX zones 1 and 2.
- Conductive multi-layer technology
- Safe against electrostatic ignition hazards according to IEC TS 60079-32-1:2013 and TRGS 727:2016
- Can be used with liquids of explosion group IIA
- Closed conductive valve body
- Easily distinguished UN and NON-UN IBC
Dimensions
The following dimensions are standardised IBCs for filling materials up to a density of 1.6 Rho
volumes | length | width | height |
---|---|---|---|
1000 | 1200 | 1000 | 1163 |
Valves
We offer integrated or replaceable valves.

Volumes | DN 50 mm | DN 80 mm |
---|---|---|
1000 |
Lid
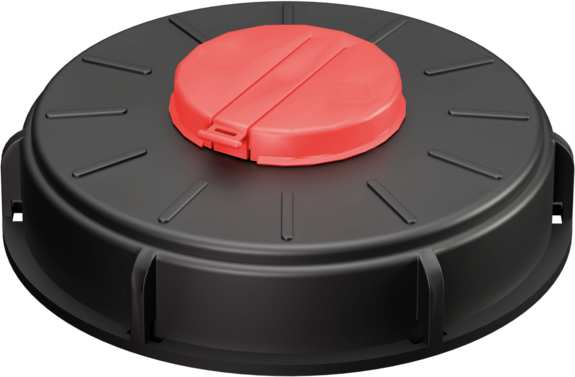
Volumes | DN 150 mm | DN 225 mm |
---|---|---|
1000 |
FAQ
Frequently Asked Questions
When potentially hazardous situations arise, EX containers are the preferred choice. The designation, sometimes referred to as “EX version,” already reflects the key characteristic – “EX” stands for “explosive” and relates to hazardous materials that are flammable and explosive. Our EX containers from the POLYex product line are suitable for use in EX zones 1 and 2, such as around trucks or storage facilities. Zone 1, the more sensitive area, is defined by the International Electrotechnical Commission (IEC) as “an area in which it is likely that an explosive atmosphere consisting of a mixture of air and flammable substances in the form of gas, vapour or mist will occur during normal operation.”
The advantages of EX containers include multilayer technology with inherent conductivity and various certifications according to IEC TS 60079-32-1:2013 and TRGS 727:2016. We ensure that all EX containers are clearly distinguishable from UN or non-certified containers. Each unit has a volume of 1,000 litres and an empty weight ranging from 59 to 63 kilograms, depending on the type of pallet integrated. With base dimensions of 1,000 x 1,200 mm, the EX container fits precisely on an industrial pallet.
Both the valve and the lid are available in different sizes. EX IBCs are manufactured from high-quality, multilayer HDPE, with a maximum density of up to 1.6 g/cm³.
To counteract occasional electrostatic build-up, all EX containers are equipped with a grounding cable. This is particularly important at the outlet, which is why the grounding feature is integrated into the outlet valve. The outlet is conductive, and the grounding cable is double-bolted – preventing it from being torn off. Additional grounding features include the ribbed plastic lid and pallet grounding via discharge plates attached to the steel tube frame.
EX containers, in particular, are subject to strict safety requirements. At WERIT, we proactively include reinforced plastic corner protectors. The advantage: forklift tines cause virtually no damage, and potential collisions are effectively cushioned. Corner protection in an IBC tank also helps prevent leakage and enhances overall safety. While not legally required, corner protection is part of our standard design and reflects state-of-the-art safety. The rest of the container is safeguarded by its multilayer structure and a galvanised steel grid frame – resulting in a highly secure product.
Not only the IBC EX containers but also the pallets themselves are grounded. This is achieved using a steel crossbar with conductive plates for direct contact with the ground. It applies to both plastic and wooden pallets and is independent of the size – suitable for both Euro and industrial pallet formats. Grounding can also be achieved via an external grounding cable if needed.
IBC EX containers must offer maximum safety. As they are used for storing and transporting explosive substances, the inner structure must be completely secure. This is ensured by using multilayer technology. The outer shell consists of several layers, with the external layer being conductive. In combination with other safety features, this provides reliable protection against electrostatic ignition risks, in accordance with IEC TS 60079-32-1:2013 and TRGS 727:2016.